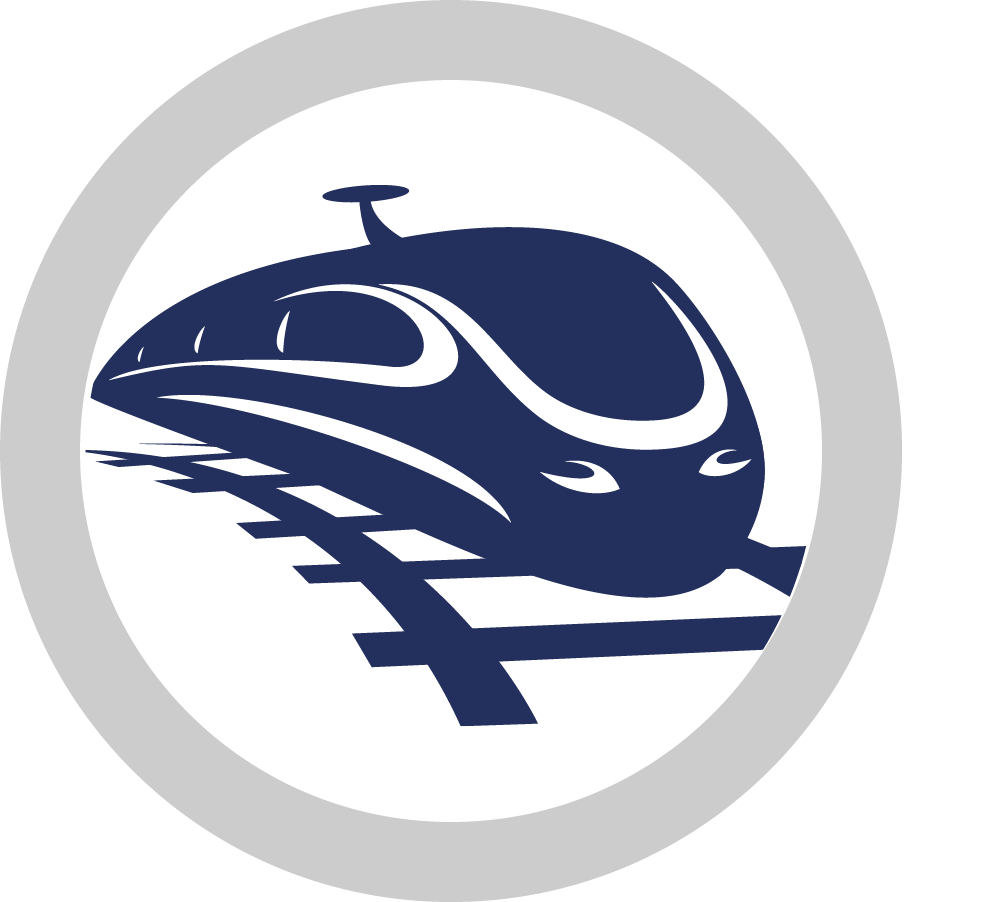
Total Train Builder Support from Unipart Rail
Train builders operate in a very competitive market. They need to meet an increasing array of demands including more reliable, lower cost rolling stock, guaranteed availability, enhanced customer experience and improved environmental performance.
More than just supplying trains they must also provide a comprehensive aftermarket customer service to lower whole-life costs of ownership.
In many markets, there are also localised manufacturing, assembly and content requirements.
Innovative Parts Provision
Increasing demands on train availability and utilisation plus the continual shrinking of maintenance windows demand new approaches to maintenance and parts provision.
Demands for localisation and the need for train builders to provide ongoing aftermarket support also requires a different supply chain approach.
Why you should use Unipart Rail?
We have numerous successful long term relationships with train operating companies. Close, collaborative partnerships with TOCs who rely on Unipart Rail to keep their trains running. We have also developed an intimate understanding of the rail industry, train operators, rolling stock, the products and technology they use and the supporting supply chain.
- An efficient consolidated supply chain combining the best of the local and international supply. A supply chain backed by safety, quality and compliance assurance across all parts and services.
- Lean operations and a more efficient supply chain for new build and maintenance operations - consolidated supply and just in time parts availability, when and where they are needed, at the point of use.
- Asset management including Condition Based Maintenance technology, overhaul and repair services and obsolescence management support to reduce cost of ownership.
- Innovative solutions to help meet operator cost, capacity, customers and carbon requirements.
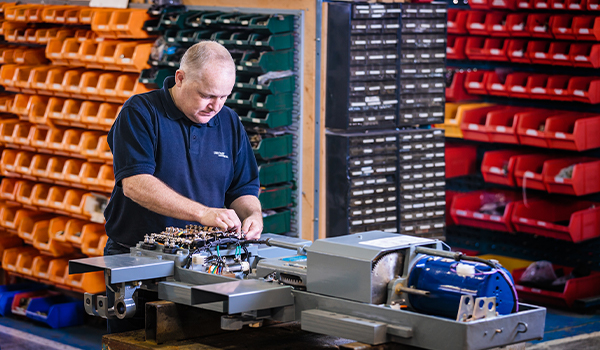
Unipart Rail’s service is underpinned by significant investment in processes, systems and a team specialising in new product development, customer service, supplier management and engineering. Our dedicated engineering team ensures supplied products are safe and meet both standards and legislative requirements.
Continual innovation and investment in people and systems sees us lead in the development of the Condition Based Supply Chain to deliver new train operator and maintenance operations efficiencies.
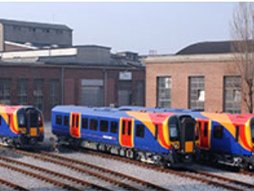
Siemens
Performance through Engagement
Siemens Traincare staff attended
Unipart Expert Practices 1 week
Lean Academy, to learn how to
implement lean tools and techniques
within their project. Results include
98% increase in material availability.
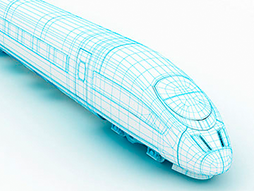
procurement activities and storage optimisation. Unipart Rail’s kitting system significantly
reduced the time taken to complete
the overhaul operation.
TPWSfour
Product Innovation
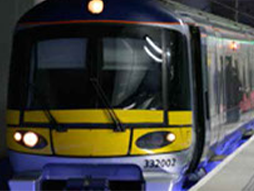
undertake a diagnostic study at their light maintenance depot stores operations.
Results included costs savings of 20% and increased material availability to 98%.
Door Diagnostics