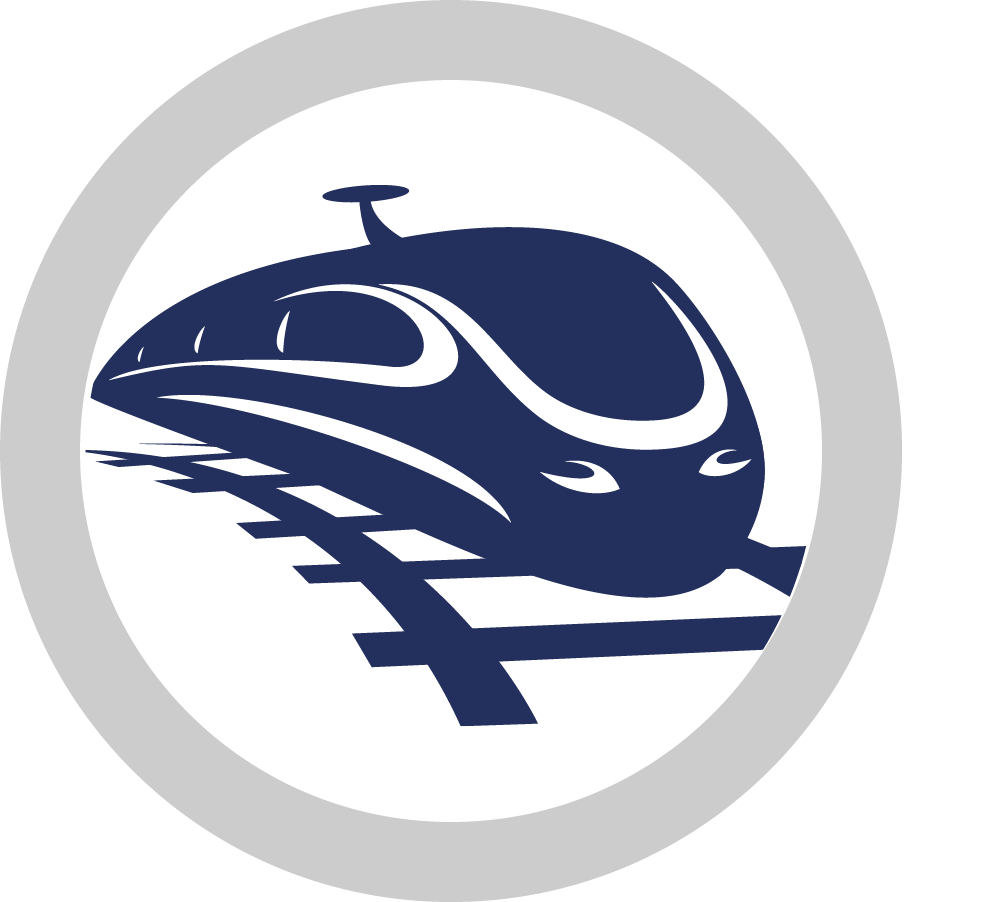
Efficiently Maximising Rolling Stock Uptime
Rolling stock needs to be cost-effective. It also needs to be operational and available. The last thing a freight and train operator needs is unavailable rolling stock.
As someone involved in the maintenance, repair and overhaul of trains, you also face the challenge of having to deliver in ever-shortening timescales and at a lower cost.
The supply chain has a major impact on the cost base of maintainers and overhaulers. It also affects their ability to meet operator demands and deliver in time. Whilst a weak supply chain threatens efficiency, an effective supply chain offers a whole number opportunities:
Challenges such as how to:
- Ensuring parts are safe and adhere to the required standards and legislation
- Managing a disparate and diverse supply chain
- Ensuring the right parts are where they need to be when they are needed
- Improving depot operations that minimise downtime
- Making the best use of condition monitoring to add real value and bring new efficiencies to train maintenance
Increasing demands on train availability and utilisation and ever shrinking maintenance windows necessitate fresh approaches to maintenance and the provision of parts.
Supply Chain Time Savings
The supply chain has a significant impact on a freight fleet operator’s ability to meet these challenges. It does though present challenges of its own:
- Ensuring parts availability across multiple suppliers and that parts adhere to the required quality, safety, regulatory standards.
- Efficient maintenance and depot operations that minimise downtime.
- Understanding and managing parts performance and its impact on overall train performance.
- Delivering new innovation to bring new efficiencies to improve customer experience.
Why you should use Unipart Rail?
We manage your depot materials operations and supply chain
to keep you service levels high and your costs low.
Continual innovation through solutions such as Smartserve, condition based maintenance and lineside maintenance improve the way you work. And because of our supply chain positioning and internal engineering excellence, all materials we supply are safety assured and accredited. Your customer’s assets always have the best materials and components – always at the right cost.
- Assurance around safety, quality and standards compliance for all parts and services.
- Lean operations and a more efficient supply chain for maintenance operations - consolidated supply and just in time parts availability, when and where they are needed, at the point of use.
- Asset management including Condition Based Maintenance technology, obsolescence management and repair and overall services that complement your services and help reduce maintenance costs.
- Innovation in technology and processes that supports improved operational and business performance
- Unipart Rail’s service is underpinned by significant investment in processes, systems and a team specialising in new product development, customer service, supplier management and engineering. Our dedicated engineering team ensures supplied products are safe and meet both standards and legislative requirements.
- Our continual innovation and investment in people and systems sees us lead in the development of the Condition Based Supply Chain to deliver new maintenance operations efficiencies.
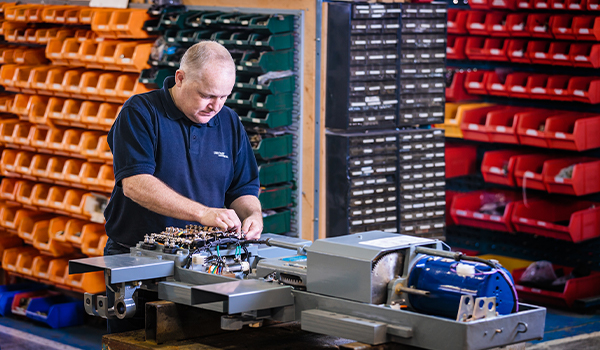
Unipart Rail’s service is underpinned by significant investment in processes, systems and a team specialising in new product development, customer service, supplier management and engineering. Our dedicated engineering team ensures supplied products are safe and meet both standards and legislative requirements.
Continual innovation and investment in people and systems sees us lead in the development of the Condition Based Supply Chain to deliver new train operator and maintenance operations efficiencies.
Case Studies...
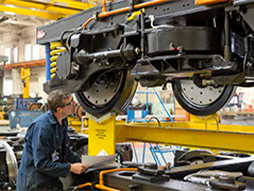
Siemens
Spares Support Bogie Overhaul
Unipart Rail was awarded a prestigious
contract to overhaul 450 Siemens Class
444 bogies over a 13 month period.
The output requirement was 10 bogies
per week within a 5 day turnaround.

TrackPan Installation
Perth Depot
used by ScotRail and Network Rail in
Perth on a new carriage wash facility,
providing a preventative measure for
waste water and other contaminants
entering the ballast, without disturbing
the track.
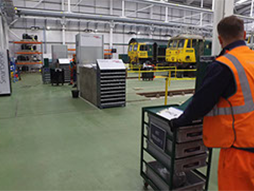
Freightliner
SmartServe Solution
they were opening a new depot and were
looking for an innovative solution that
would support their maintenance activities. Unipart Rail’s SmartServe solution provides a flexible and scalable solution that can be fine-tuned to customer requirements.