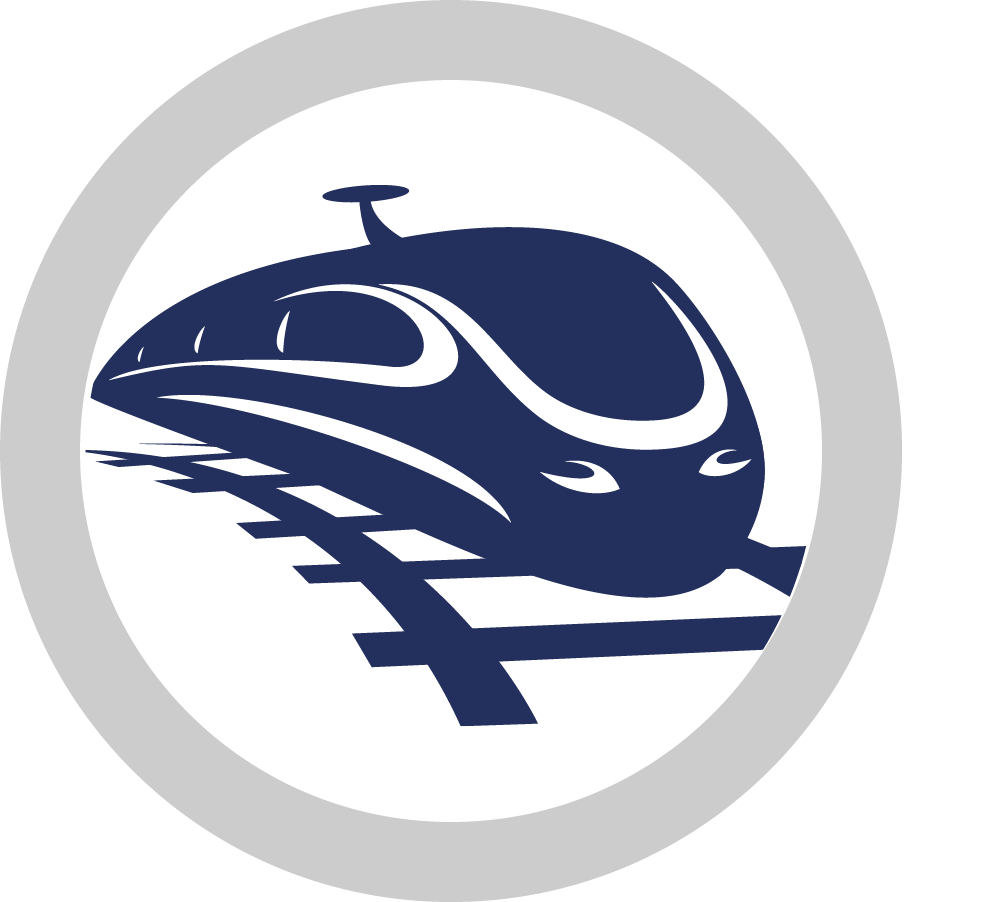
The Challenges Of Modern Fleet Management
Making sure that your fleet is safe, reliable, cost effective, and an attractive proposition for train operators is a constant challenge.
Challenges such as how to:
- drive competitiveness to keep you and your clients profitable
- meet train operator demands and keep your fleets an attractive proposition
- deal with the threats and opportunities posed by innovation
- improve train reliability and availability
- enhance your fleet’s residual value
- meet legislative requirements
- handle obsolescence
We recognise that these essential technical, logistical and management performance challenges can draw heavily on limited internal resources and demand new efficiencies and innovation from the supply chain.
Why you should use Unipart Rail?
Support That Delivers Ongoing Value to Rolling Stock Operators and Train Operating Companies
Experienced in working alongside the world’s leading rolling stock leasing companies and train operating companies, we understand your business intimately.
We know your challenges. We understand them. And we know exactly what it takes to meet them, to deliver long-lasting and profitable fleet support.
- Assurance around safety, quality and standards compliance for all parts and services.
- Asset Management including Condition Based Maintenance technology and Obsolescence Management support to reduce cost of ownership for operators and maintains fleet viability.
- Innovation that addresses important issues around carbon, capacity, cost and customer experience.
- Lean operations and an efficient consolidated supply chain ensuring parts are available when and where they are needed to maximise train uptime and availability.
- Continued Service Operation (CSO) – identification and support around those risk parts needed to keep trains in operation till the end of lease.
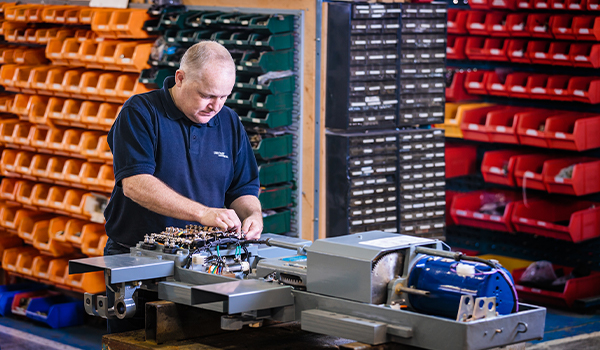
Unipart Rail’s service is underpinned by significant investment in processes, systems and a team specialising in new product development, customer service, supplier management and engineering. Our dedicated engineering team ensures supplied products are safe and meet standards and legislative requirements.
Our continual innovation and investment in people and systems see us lead in the development of the Condition Based Supply Chain to deliver new train operator and maintenance operations efficiencies.
Case Studies...
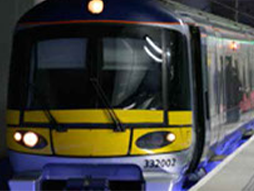
Door
Diagnostics
remote monitoring of train doors through
the use of inductively coupled telemetry.
It is a low cost solution that delivers “health indicators” on the doors that allow effective
and targeted interventions to be made.

has been proven in service to improve
reliability, reduce power consumption,
reduce mass and reduce potential
failure modes.
Code
Conversion Unit

of materials that would reduce time, procurement activities and storage optimisation. Unipart Rail’s kitting system significantly reduced the
time taken to complete the overhaul operation.
Eurostar
Re-usable kitting solution